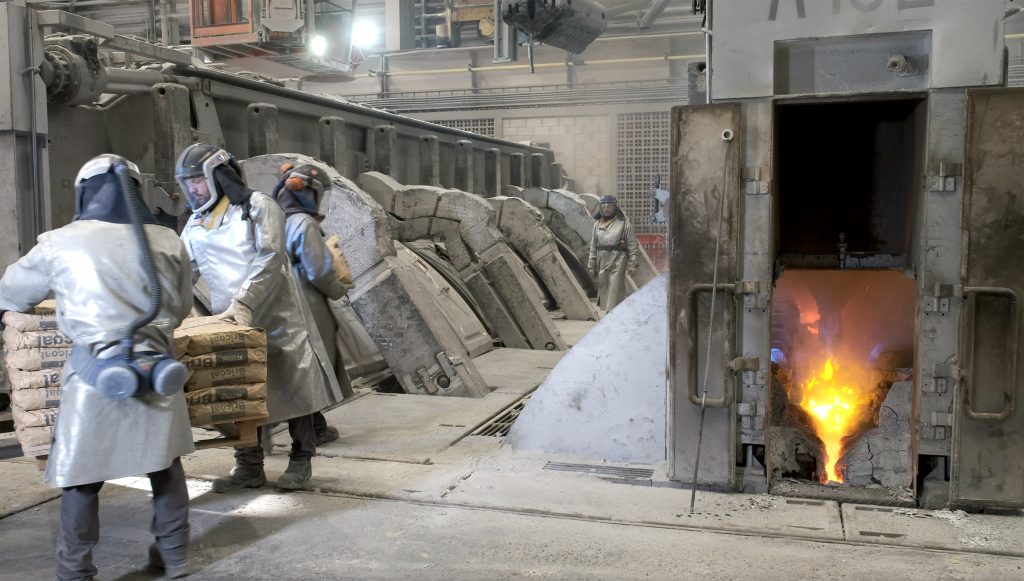
Construction of a first furnace using recycled metal
Aluminium Dunkerque is building a new high energy efficient furnace that will be used to produce an additional 20,000 tonnes of aluminium alloy ingots per year, of which 7,000 tonnes of metal from waste recycling.
The project has funding of €1.5m from the France 2030 programme. It will allow us to achieve significant recycling volumes, and thus to meet the increasingly high expectations of our automotive customers committed to a decarbonisation strategy.
The overall ecological footprint of ingot production will thus be improved:
- Reduction in CO2 emissions: -10% on average per tonne of aluminium produced
- Energy savings: -96kWh/year
The ultimate aim is for our total ingot production to contain an average of 10% recycled metal. Integration work is under way, and furnace construction will begin in the summer of 2024, with commissioning scheduled for early 2025.
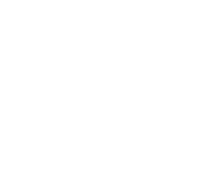
Continued installation of extractor hoods in the Foundry
When finishing metal is added to foundry furnaces to produce alloys, dust escapes through the doors.
To remedy this, extractor hoods are being installed over the installations to improve air quality in the Foundry and prevent the equipment from deteriorating. This project will also make it possible to reduce our diffuse emissions.
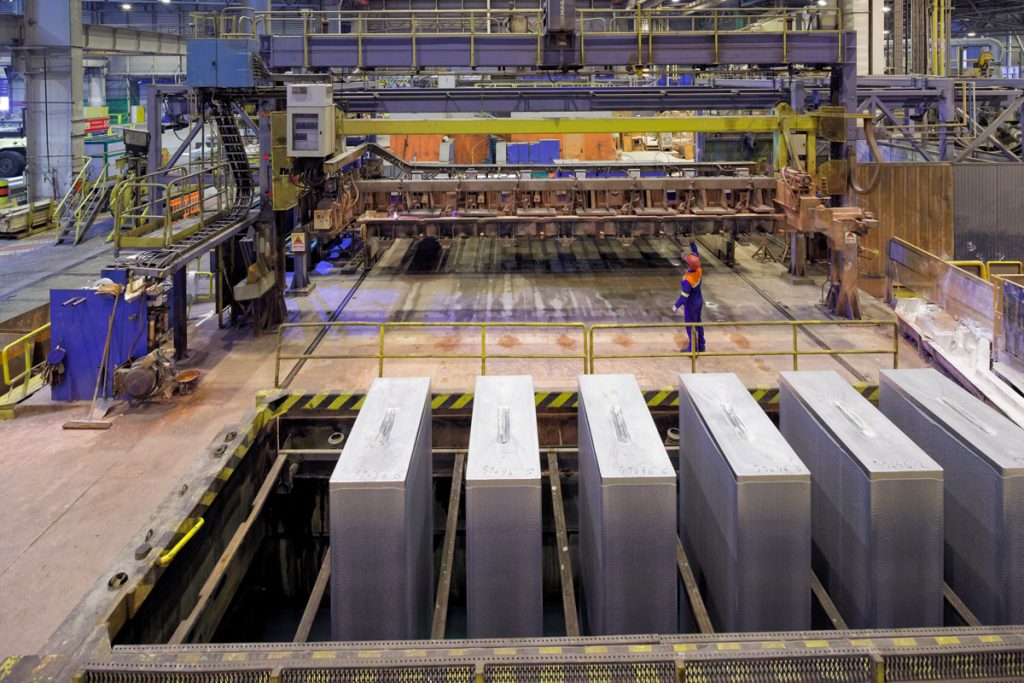
Construction of a photovoltaic power plant
Aluminium Dunkerque
is already a world leading low carbon aluminium producer
Building on these strengths, we are stepping up our energy and environmental transition in line with the COP21 objectives and as part of the Energy Transition Contract we signed with the French government on 22 November 2023.
It is against this backdrop of site decarbonisation coupled with the need to secure our electricity supply, and the draft law on the acceleration of renewable energies, that Aluminium Dunkerque is going to build a photovoltaic power plant on its site.
The aim is to cover all the company’s car parks with solar panels for direct on site self-consumption. The plant will be connected to the high-voltage substation in the Foundry and will produce 3,200 MWh/year.
Creation of an internal heating loop
To further reduce its heating energy consumption, Aluminium Dunkerque is going to create an internal heating loop using its unavoidable heat emissions.
Heat will be captured from the air compressor cooling circuits using using an exchanger on each compressor. A heat pump will raise the temperature to heat the central areas, the warehouse and the domestic hot water.
In addition to this heating loop, a cooling unit will be installed to cool the compressors and the central patio areas in summer. Energy recovery will be possible on this cooling unit; it will provide heating power for domestic hot water.
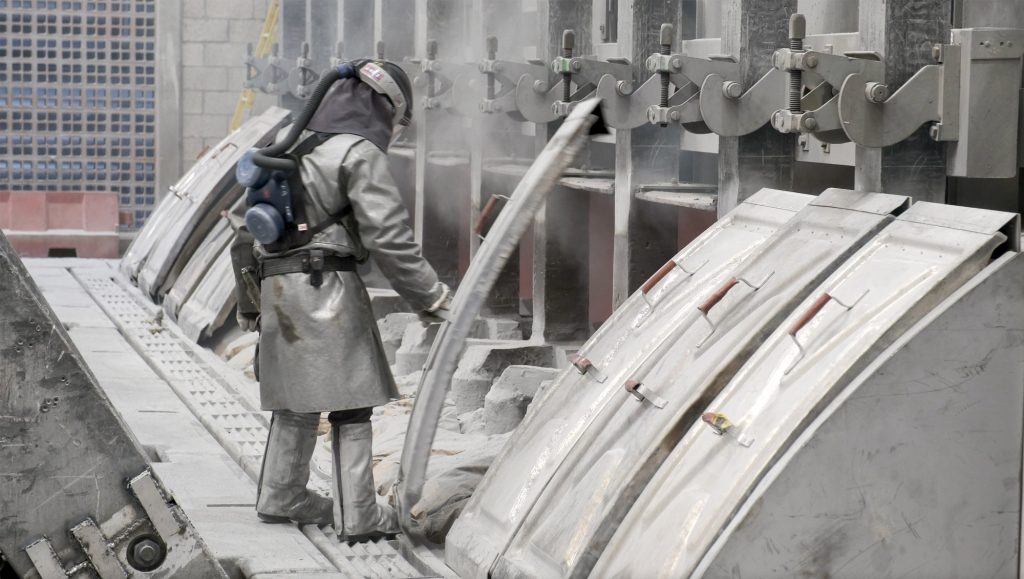
A 3rd generation of anode and metal transport vehicles
The machinery used to transport anodes and hot metal is specific to the aluminium industry, and even to Aluminium Dunkerque since the foundry furnaces on our site are loaded by emptying the ladles of liquid aluminium directly from the machinery.
The fleet is renewed every 10 to 12 years. The vehicles are designed by a specialist manufacturer who adapts them to the constraints of our activity as well as to European legislative requirements. The new HENCON vehicles, the 3rd generation of machinery on our site, were commissioned in 2023 after a 6-month reliability testing period.
They are especially characterised by the inclusion of new safety technologies: rear detection sensors, 360° camera, speed reduction on bends, flexible solid tyres to avoid the risk of explosion, and improved visibility thanks to a fully glazed cabin. The machinery is also now fitted with hydraulic rather than mechanical suspension for better comfort.
C4Capture Project
teamwork to adapt carbon capture technology to the aluminium industry
By 2030, Aluminium Dunkerque aims to reduce its overall greenhouse gas emissions by 30% and its direct emissions in particular, by 59%.
These targets especially mean adapting carbon capture to the aluminium industry. This technology will make it possible to reduce the site’s emissions by 250 kt of CO2eq by 2030 by capitalising on the dynamics of the Dunkirk hub.
With this in mind, Aluminium Dunkerque is a stakeholder in the C4Capture project: “Collaboration pour la Concentration et la Capture de CO2 dans la filière aluminium”. This project, in which Trimet, Rio Tinto Aluminium and Fives are also participants, aims to demonstrate the feasibility of adapting carbon capture technology to the primary aluminium production sector.
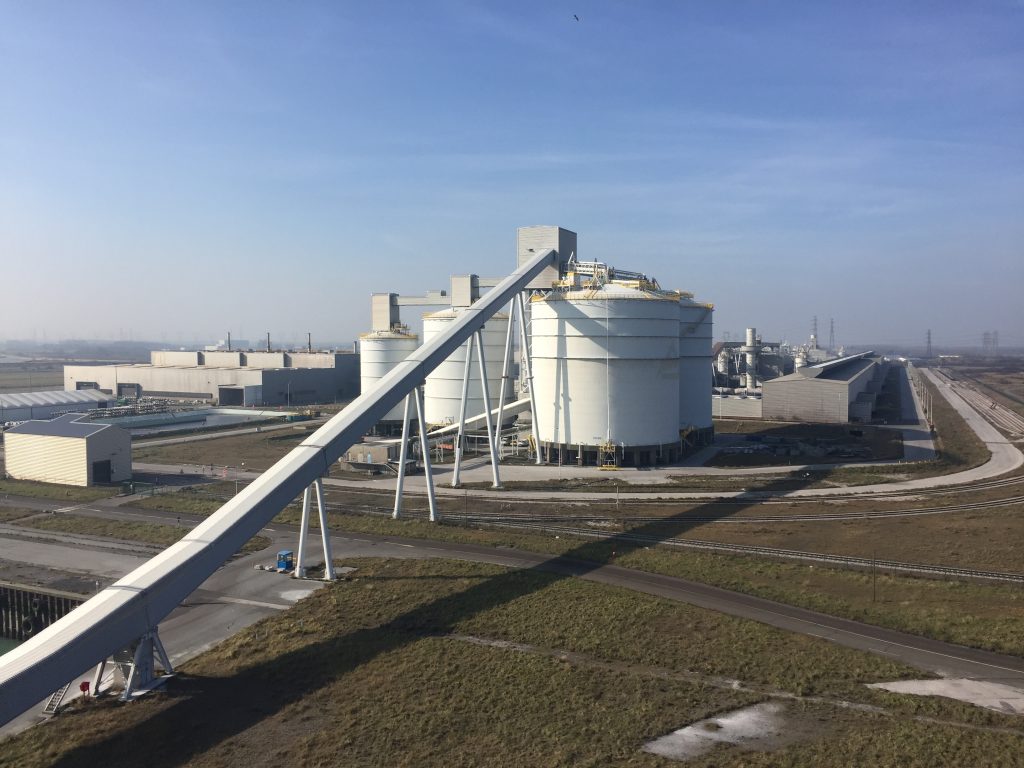